Михаил Нижник, генеральный директор, ООО «Группа МЕТТАТРОН»
Александр Черный, технолог, ООО «Группа МЕТТАТРОН»
В четвертой части цикла систематизируются дефекты, возникающие при монтаже печатных плат, причины их возникновения и способы предотвращения.
Рекомендации основаны на результатах исследований фирмы «KOKI», Япония.
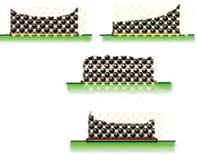
Рис. 49. Дефекты печати —
соскабливание, избыток пасты,
«хвосты»
ДЕФЕКТЫ ПЕЧАТИ
Типичные проблемы при работе с паяльными пастами, их причины и методы устранения.
Затекание пасты под трафарет при его загрязнении или деформации: при непрерывной печати паста затекает под трафарет, что вызывает образование шариков припоя и перемычек (см. рис. 50). Хотя степень затекания, в основном, определяется реологией паяльной пасты, корректировка следующих параметров позволит предотвратить появление данного дефекта:
— уменьшите давление ракеля до минимально необходимого, чтобы при проходе ракеля трафарет полностью очищался от паяльной пасты;
— проверьте точность совмещения апертур с контактными площадками;
— проверьте натяжение трафарета и равномерность прилегания к плате;
— откорректируйте апертуры в трафарете в сторону уменьшения (меньше размера контактной площадки);
— снизьте температуру в рабочем помещении: это повысит вязкость пасты;
— чаще производите очистку трафарета, при этом используйте специальные безворсовые материалы и отмывочные жидкости;
— обеспечьте надежную фиксацию печатных плат при нанесении паяльной пасты;
— снизьте скорость движения ракеля, если она без надобности слишком высока, поскольку это уменьшает тиксотропность пасты и делает её менее вязкой.
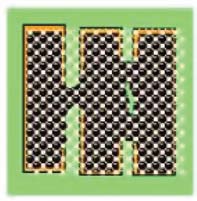
Рис. 50. Дефекты печати —
затекание пасты под трафарет
Паяльная паста остается в апертурах после отделения трафарета от печатной платы:
— проверьте, правильно ли подобрана толщина трафарета: возможно, площадь стенок апертур значительно больше площади контактных площадок, то есть конструкция апертур не соответствует стандарту IPC-7525;
— проверьте, правильно ли подобрана паяльная паста по типу зерна;
— отрегулируйте скорость отделения трафарета от печатной платы: возможно, она слишком высокая на начальном этапе;
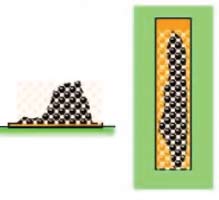
Рис. 51. Дефекты печати —
недостаточное количество пасты
При нанесении паяльной пасты образуются перемычки:
— проверьте натяжение трафарета на раме и не деформирован ли он;
— если паста слишком вязкая, проконтролируйте температуру помещения, снизьте скорость перемещения ракеля. Если это не помогло, замените пасту;
— если размер апертур равен размеру контактных площадок, замените трафарет и проследите, чтобы размер апертур составлял 75―90% от размера площадок.
Неравномерные отпечатки паяльной пасты из-за плохого отделения пасты от апертур:
— проверьте скорость отделения трафарета от платы, чистоту трафарета и качество паяльной пасты.
— увеличьте давление и скорость перемещения ракеля для уменьшения вязкости.
— если дефекты расположены локально, проверьте фиксацию и плоскостность плат.
Соскабливание: давление ракеля слишком высоко, и он соскабливает верхнюю часть нанесенной пасты (см. рис. 49):
— отрегулируйте давление до минимально допустимого уровня;
— используйте металлический ракель;
— если размер апертуры больше 2×2 мм, замените трафарет, разделив большие апертуры на маленькие перемычками шириной 0,2 мм.
Избыточное количество пасты на контактных площадках:
— увеличьте давление ракеля;
— если кромка ракеля истерлась, замените ракель;
— устраните зазор между трафаретом и платой;
— обеспечьте надежную фиксацию печатных плат при нанесении пасты;
— замените трафарет на более тонкий;
— если отпечаток паяльной пасты больше размера контактной площадки, проверьте размер апертур.
«Хвосты» и приподнятые кромки:
— слишком высока скорость отделения трафарета. Уменьшите скорость отделения трафарета до минимально необходимой.
Смазанные края отпечатков паяльной пасты:
— печатная плата или трафарет сместились в процессе разделения, отрегулируйте этот процесс.
Смазывание отпечатков паяльной пасты после нанесения. Велик уровень вибрации при перемещении печатных плат от принтера до установщика:
— проверьте уровень вибрации на конвейере;
— в случае ручного переноса используйте специальную тару.
Растекание отпечатков паяльной пасты после нанесения:
— тщательно перемешайте пасту в течение минуты шпателем или в специальном миксере;
— поддерживайте в помещении температуру 20-25 °C и влажность 50–60%.
Смещение отпечатков паяльной пасты после нанесения:
— проконтролируйте точность совмещения трафарета с печатной платой.
Остатки паяльной пасты на печатной плате. Из-за этого в непредсказуемых местах возникают шарики припоя:
— чаще мойте трафарет;
— отмойте забракованные печатные платы погружением в раствор с последующим струйным ополаскиванием.
На подложку наносится недостаточное количество пасты — меньше 80% объема апертуры (см. рис. 51):
— недостаточное количество пасты на трафарете. Диаметр валика пасты должен находиться в пределах от 12,5 до 25 мм;
— слишком высокое давление ракеля, из-за которого апертуры забиваются;
— высыхание пасты на трафарете. Своевременно добавляйте свежую пасту на трафарет;
— неправильно подобрана паяльная паста по типу зерна. По минимальному габариту апертуры должно умещаться не менее 5 самых крупных зерен (рекомендовано — от 8).
Высыхание паяльной пасты:
— если паста очень быстро высыхает на трафарете, проверьте ее срок годности и температуру окружающей среды;
— направленный на трафарет поток воздуха из системы вентиляции ускоряет испарение флюса. Используйте защитные экраны.
Неправильная форма или недостаточное количество пасты в отверстиях для штыревых выводов: проверьте конструкцию трафарета на соответствие IPC-7525.
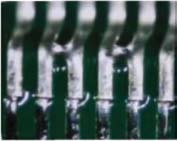
Рис. 52. Дефекты пайки — перемычки
ДЕФЕКТЫ ПАЙКИ
Перемычки и мостики припоя:
— на площадки подается слишком много пасты (см. рис. 52). Желательно уменьшить размер апертуры с учетом растяжения трафарета, степени осадки пасты, точности совмещения при печати. Примеры: если шаг элементов — 0,5 мм, ширина площадки 0,25 мм, ширина апертуры должна быть равна 0,235 мм. Если шаг элементов — 0,4 мм, ширина площадки 0,2 мм, то ширина апертуры — 0,185 мм;
— несовпадение местоположения компонентов и пасты (см. рис. 53);
— загрязнение печатной платы — чаще очищайте нижнюю сторону трафарета;
— слишком глубокая посадка компонентов (см. рис. 54). Отрегулируйте высоту сброса компонента установщиком.
— осадка паяльной пасты. Слишком большое напряжение сдвига из-за высокой скорости ракеля нарушает тиксотропные свойства пасты, и она теряет стойкость к осадке. С другой стороны, если температура в помещении выше 30°С, то вязкость пасты падает, и она также будет давать осадку. Снизьте скорость ракеля; температура в рабочем помещении должна быть в пределах 25±2,5°С;
— образование перемычек под корпусом чип-элементов и бусинок припоя сбоку от чип-элементов из-за неправильной формы апертур. Корректируем апертуры, чтобы уменьшить количество пасты.
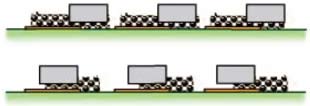
Рис. 53. Несовпадение компонентов и площадок с пастой

Рис. 54. Слишком глубокая посадка компонентов
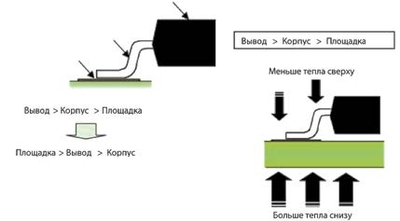
Рис. 55. Капиллярный подсос
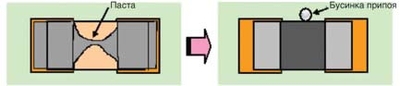
Рис. 56. Образование бусинок припоя
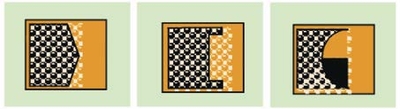
Рис. 57. Уменьшение размеров апертур трафарета для сокращения
количества пасты
Образование бусинок припоя:
— уменьшите количество паяльной пасты, наносимой на контактные площадки;
— уменьшите давление при установке чип-компонентов;
— используйте специальную конструкцию апертур (см. стандарт IPC-7525);
— обеспечьте плавный набор температуры в зоне предварительного нагрева.
Образование шариков припоя (рис. 58). В эту группу входит пять дефектов.
— Шарики припоя возле выводов компонента могут появиться в результате неточного совмещения платы и трафарета и чрезмерного количества пасты, нанесенной на контактные площадки. Обеспечьте точное совмещение апертур с контактными площадками и/или уменьшите количество пасты.
— Крупные шарики припоя рядом с контактными площадками. Это происходит из-за выдавливания паяльной пасты при установке компонента и ее осадке. Уменьшите толщину трафарета и/или размер апертур, проверьте настройки установщика.
— Шарики припоя на контактных площадках и паяное соединение с низкой механической надежностью. Это говорит о неправильном выборе паяльной пасты. Замените пасту и проведите испытания на шарики припоя (IPC-TM-650, метод 2.4.43), а также поддерживайте влажность в рабочем помещении в пределах 30–70%.
— Хорошая смачиваемость контактных площадок и плохая смачиваемость выводов компонентов. Снизьте температуру сушки компонентов до 60 °C, чтобы выводы компонентов не так сильно окислялись.
— Единичные шарики на очень большом расстоянии от ближайшего компонента. Паста попадает туда из-за плохой очистки нижней стороны трафарета.
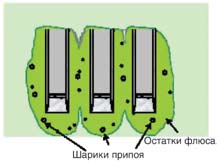
Рис. 58. Микросферы припоя
Выворачивание компонентов — эффект «надгробного камня» (tombstoning). Причина: на одной контактной площадке компонента припой уже расплавился, а на другой — еще нет. Сила поверхностного натяжения, возникшая на капле расплавленного припоя, заставляет подняться один из торцов чип-компонента над контактной площадкой (рис. 60).
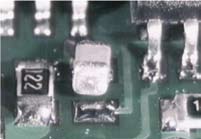
Рис. 59. Выворачивание,
поднятие компонентов
Влияющие на выворачивание факторы:
— неправильный размер апертур;
— неаккуратное размещение компонентов при монтаже;
— несоответствие объема наносимой пасты размеру площадки;
— разная смачиваемость у разных выводов одного компонента в случае их чрезмерного окисления или высокой загрязненности;
— ошибки при конструировании печатной платы.

Рис. 60. Силы, действующие на компонент при выворачивании: Т1 — момент силы веса компонента; Т2 — момент сил натяжения расплавленного припоя под компонентом; Т3 — момент сил натяжения расплавленного припоя на боковой стенке компонента. Условие, при котором происходит выворачивание: Т1 + Т2 < Т3
Способы решения проблемы:
— скорректируйте размер апертур и толщину трафарета;
— перенастроить установщик компонентов;
— при отсутствии термобарьеров либо проводите пайку в ручном режиме, либо увеличьте время нахождения печатной платы в зоне предварительного нагрева, чтобы «полигон» металла нагрелся до необходимой температуры. Но это вряд ли удастся, так как чрезмерное время нахождения в зоне предварительного нагрева приводит к полному выкипанию флюса с контактных площадок малого размера;
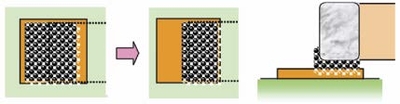
Рис. 61. Уменьшение количества пасты позволяет
решить проблему выворачивания компонента
— Регулировка времени смачивания компонента припоем. Как только эвтектический сплав (Sn63/Pb37) переходит в расплавленное состояние, он сразу же начинает смачивать выводы компонента. Поэтому, если выводы по разные стороны компонента начинают смачиватся неодновременно, возникает опрокидывающий момент Т3, который и выворачивает компонент.
Если ввести в припой некоторое количество сурьмы (Sb), он будет переходить из твердого состояния в жидкое через промежуточное пластическое состояние, что поможет предотвратить появление дефекта. В таком пластическом состоянии, даже если оно возникнет на одной стороне компонента, смачивание начинается не сразу, а спустя некоторое время, за которое на другой стороне тоже наступает пластические состояние
— это и синхронизирует момент начала смачивания. Фирма «KOKI» разработала сплав SSA с составом: 62,6 Sn; 36,8 Pb; 0,4 Ag и 0,2 Sb. Сплав SSA предотвращает выворачивание компонентов, потому что корректирует время начала смачивания и уменьшает силу поверхностного натяжения.
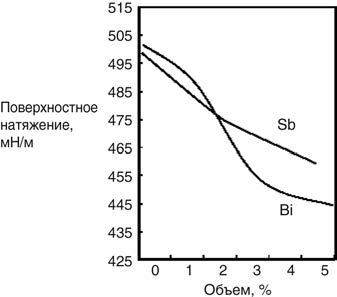
Рис. 62. Снижение поверхностного натяжения
добавкой висмута
Плохая смачиваемость контактных площадок с неравномерным распределением припоя:
— перед началом сборки промойте печатные платы специальной жидкостью;
— если причина в слишком тонком покрытии HASL, предъявите претензии поставщику плат.
Плохая смачиваемость контактных площадок и выводов компонентов:
— понизьте температуру пайки, чтобы флюс не выгорал и паяемые поверхности не окислялись повторно;
— уменьшите время пребывания выше температуры плавления до 30–90 с;
— уменьшите стадию предварительного нагрева (не более 120 с), чтобы флюс не истощался;
— увеличьте количество паяльной пасты.
Плохая паяемость контактных площадок с покрытием ENIG:
— нарушены условия хранения: печатные платы должны храниться в вакуумной упаковке в шкафах сухого хранения при температуре 25 °C и влажности 10%. Срок хранения не должен превышать 6 месяцев с даты производства;
— изготовитель печатных плат нанес золото по окисленному никелю. Проведите входной контроль паяемости в соответствии с требованиями стандарта J-STD-003. В случае несоответствия предъявите претензии изготовителю.
После пайки паста не оплавилась и осталась в виде массы отдельных шариков припоя:
— уменьшите стадию предварительного нагрева (не более 120 с), чтобы флюс не истощался;
— если используется паста с истекшим сроком годности или паяльная паста хранилась с нарушениями условий хранения, проведите испытания пасты «на шарики припоя» согласно IPC-TM-650, метод 2.4.43. Если паста покажет плохие результаты, замените ее.
— сократите межоперационные интервалы.
Бугристые, неровные, матовые паяные соединения на отдельных крупных выводах микросхем:
— настройте температуру и время на стадиях предварительного нагрева и пайки так, чтобы крупные теплоемкие компоненты успели прогреться;
— предотвратите вибрацию конвейера печи в процессе пайки.
Отдельные выводы компонентов приподняты над галтелью припоя:
— обеспечьте равномерное нанесение пасты на контактные площадки;
— откорректируйте давление при установке компонентов.
Отсутствие контакта отдельных выводов компонентов с оплавленным припоем из-за деформации выводов или некомпланарности поверхности контактных площадок. Чаще всего дефект наблюдается на компонентах с малым шагом:
— проверьте компланарность выводов перед установкой;
— исключите ручные операции установки компонентов;
— проверьте равномерность металлизации, используйте печатные платы с покрытием ENIG.
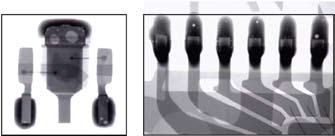
Рис. 63. Пустоты в пайке
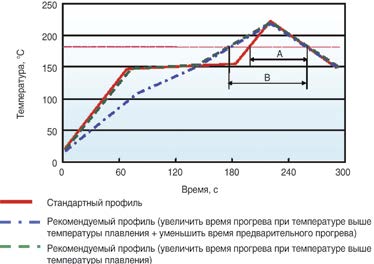
Рис. 64. Устранение пустот коррекцией термопрофиля
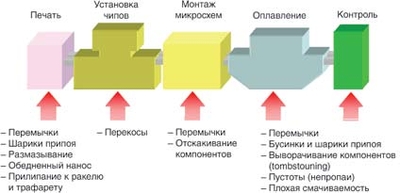
Рис. 65. Основные дефекты, возникающие на технологических
операциях
Пустоты в паяных соединениях:
— обеспечьте медленное повышение температуры на стадии предварительного нагрева (0,5–1,5ºС/с), чтобы паста не разбрызгивалась в результате закипания флюса;
— повысьте температуру пайки;
— уменьшите количество паяльной пасты на контактных площадках.
СПЕЦИФИЧЕСКИЕ ДЕФЕКТЫ, ВОЗНИКАЮЩИЕ ПРИ МОНТАЖЕ МИКРОСХЕМ В КОРПУСАХ BGA И PGA
Дефект «голова на подушке»:
— паяльная паста оплавилась не полностью, поверхность паяного соединения шероховатая и повторяет форму частиц паяльной пасты. Откорректируйте температурный профиль на стадиях предварительного нагрева и/или пайки.
Трещины и разрывы в паяном соединении:
— повысьте температуру или время пайки.
Трещины и разрывы между шариком и подложкой микросхемы:
— снизьте скорость охлаждения после пайки.
Окисление паяного соединения (косметический дефект):
— уменьшите температуру и/или время пайки.
Коллапс шариковых выводов:
— обратите внимание на материал выводов BGA. Если это сплав SnPb, то и паяльная паста, используемая при пайке этой микросхемы, должна быть из того же сплава. Уменьшение высоты шариковых выводов на 25% — предельно допустимое;
— ограничьте растекание припоя паяльной маской согласно IPC-7095A.
«Холодная пайка» — низкая электрическая и механическая прочность паяного соединения, увеличение сопротивления контактов:
— увеличьте температуру пайки.
Деформация или деструкция паяных соединений:
— предотвратите вибрацию конвейера печи;
— снизьте скорость охлаждения согласно стандарту J-STD-020;
— используйте качественные материалы для печатных плат (температура стеклования диэлектрика должна составлять не менее 150С);
— при конструировании печатных плат руководствуйтесь стандартами IPC-7095 и IPC-7351.
Бугристые, неровные, матовые паяные соединения:
— уменьшите температуру пайки, чтобы шариковые выводы не перегревались;
— предотвратите вибрацию конвейера печи в процессе пайки.
Советуем прочитать:
Паяльные пасты: Все о главном. Часть 1
Паяльные пасты: Все о главном. Часть 2